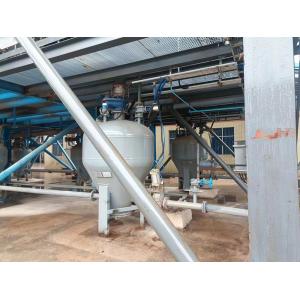
Add to Cart
Fly Ash Conveying Silo Pump / High Degree of Automation / Dense Phase Pneumatic Conveying Equipment
Description
Introduction to silo pneumatic conveying pump:
The silo pneumatic conveying pump adopts a positive pressure pneumatic conveying method to transport powdered materials, and is widely used in the transportation of materials such as fly ash, cement, cement raw materials, mineral powder, etc. in power plants.
This equipment adopts a PLC control system, which can be automatically or manually controlled. After long-term practical operation, it has been proven that the equipment has stable performance, reliable quality, and no dust pollution during transportation. It is an ideal pneumatic conveying equipment.
The transportation pipeline can be flexibly arranged according to the terrain conditions, achieving centralized, dispersed, high altitude, and long-distance transportation. The transportation process is not affected by natural conditions, ensuring that materials are not affected by moisture and are environmentally friendly and pollution-free.
Features:
The bin type conveying pump is a system that uses an air compressor as the air source, forming a high-pressure dense phase conveying state. It has the characteristics of low flow rate, low wear, and low air consumption. The single bin pump achieves intermittent conveying, while the double bin pump can achieve continuous conveying.
The warehouse pump feeding system needs to achieve a specific conveying form and has unique requirements for the characteristics of the material. It must be powder and have good flowability, and different media need to adjust different gas quantities and pressures.
The configuration of the warehouse pump feeding system is relatively complex, including inlet valve, outlet valve, exhaust valve, pressure gauge, material level gauge, intake valve group, pressure regulating valve group, control system, etc. It is a highly automated and integrated feeding system.
Large Capacity Pneumatic Conveying Bin Pump Parameter Table
Conveying Material | Bulk Density (t/m3) | Model | PCD24/H | PCD26/H | PCD28/H | PCD30/H | Conveying Distance | |
Specification | 16~20m3 | 18~22m3 | 20~27m3 | 26~32m3 | Level (m) | Level (m) | ||
Pulverized Coal | 0.5 | Delivery Volume (t/h) | 50~80 | 60~90 | 65~110 | 80~130 | 200 | 20 |
Fly Ash | 0.75 | 75~125 | 85~130 | 95~160 | 125~190 | 200 | 20 | |
Limestone Powder/Mineral Powder | 0.8 | 80~130 | 90~140 | 100~170 | 130~200 | 200 | 20 | |
Cement/Raw Meal | 1 | 100~150 | 115~175 | 130~215 | 165~260 | 200 | 20 |
Long-distance Pneumatic Conveying Bin Pump Parameter Table
Conveying Material | Bulk Density (t/m3) | Model | PCD24/L | PCD26/L | PCD28/L | PCD30/L | Conveying Distance | |
Specification | 16~20m3 | 18~22m3 | 20~27m3 | 26~32m3 | Level (m) | Level (m) | ||
Pulverized Coal | 0.5 | Delivery Volume (t/h) | 20~40 | 25~45 | 30~55 | 45~65 | 1000 | 25 |
Fly Ash | 0.75 | 35~60 | 45~65 | 45~80 | 65~95 | 1000 | 25 | |
Limestone Powder/Mineral Powder | 0.8 | 40~65 | 45~70 | 50~85 | 70~100 | 1000 | 25 | |
Cement/Raw Meal | 1 | 50~80 | 55~90 | 65~110 | 90~120 | 1000 | 25 |
Conventional Grid Pneumatic Conveying Bin Pump Parameter Table
Conveying Material | Bulk Density(t/m3) | Model | PCD18/N | PCD20/N | PCD20/N | Reference Conveying Distance | |
Specification | 5.0~6.7m3 | 7.0~10.0m3 | 10.0~15.0m3 | Level (m) | Vertical (m) | ||
Pulverized Coal | 0.5 | Delivery Volume (t/h) | 12~20 | 16~32 | 25~50 | 500 | 30 |
Fly Ash | 0.75 | 18~32 | 25~48 | 35~70 | 50 | ||
Limestone Powder/Mineral Powder | 0.8 | 20~35 | 26~51 | 38~75 | 500 | 30 | |
Cement/Raw Meal | 1.0 | 24~42 | 32~65 | 48~95 | 500 | 30 | |
Silicon Powder | 1.2 | 28~50 | 40~75 | 55~115 | 500 | 30 |
Parameter Table Of Small Size Pneumatic Conveying Bunker Pump
Material | Bulk Density(t/m3) | Model | PCD08/M | PCD10/M | PCD12/M | PCD14/M | Reference Conveying Distance | |
Specification | 0.2~0.5m3 | 0.6~1.6m3 | 1.5~2.5m3 | 2.5~5.0m3 | Level (m) | Vertical (m) | ||
Pulverized Coal | 0.5 | Delivery Volume (t/h) | 0.5~1.8 | 1.5~5.5 | 5.0~9.0 | 8.0~18.0 | 100 | 20 |
Fly Ash | 0.75 | 0.9~2.8 | 2.5~8.5 | 7.0~14.0 | 12.0~27.0 | 100 | 20 | |
Limestone Powder/Mineral Powder | 0.8 | 1.0~3.0 | 3.0~9.0 | 8.0~15.0 | 12.0~28.0 | 100 | 20 | |
Cement/Raw Meal | 1.0 | 1.2~3.5 | 3.5~11.5 | 10.0~18.0 | 16.0~36.0 | 100 | 20 | |
Silicon Powder | 1.2 | 1.5~4.0 | 4.5~13.5 | 12.0~20.0 | 19.0~43.0 | 100 | 20 |
Working principle of bin pump:
The working process of the bin pump is divided into four stages:
Feeding stage: The feeding valve and exhaust valve are opened, and the material freely falls into the pump body. When the material is full, the level gauge sends a signal, and the feeding valve and exhaust valve automatically close to complete the feeding process;
Fluidization and pressurization stage: Open the intake valve, compressed air enters the upper and bottom of the pump body, pressurizes the upper part, and diffuses the lower air through the fluidized bed, causing the material to be in a fluidized state, while the pressure inside the pump increases;
Transportation stage: When the pressure inside the pump reaches a certain value, the pressure gauge or pressure switch sends a signal, and the discharge valve automatically opens. The material fluidization on the fluidized bed strengthens, and transportation begins. The material inside the pump gradually decreases. At this time, the material on the fluidized bed is always in a state of fluidization and transportation;
Purging stage: When the material in the pump is delivered and the pressure drops to the resistance of the pipeline, the pressure gauge or pressure switch sends a signal, and the ventilation continues for a certain time. Compressed air is used to clean the pipeline, and then the inlet valve is closed. At a certain interval, the discharge valve is closed, and the inlet valve is opened to complete a conveying cycle.
Packaging and delivery
1. Standard packaging.
2. A well-trained and disciplined packaging team.
3. After sales service. After receiving the product, if you have any questions or questions, please feel free to contact us at any time. The problem will be resolved immediately for you.
4. Experienced and professional logistics agents.