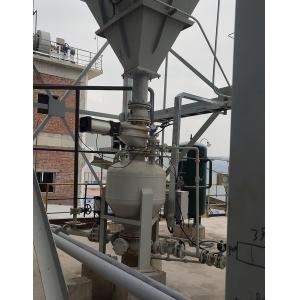
Add to Cart
Pneumatic Conveying Systems - Pressure Pneumatic Conveying Systems Manufacturer From PCD Pneumatic Conveying Equipment
Product Introduction:
Pneumatic conveying silo pump
Bin pump, also known as bin pump or hidden pneumatic conveying pump, is a relatively reliable dense phase pneumatic conveying device for conveying powder materials under high pressure. The silo pneumatic conveying pump adopts a positive pressure pneumatic conveying method to transport powdered materials, and is widely used in the transportation of materials such as fly ash, cement, cement raw materials, mineral powder, etc. in power plants. The transportation pipeline can be flexibly arranged according to the terrain conditions, achieving centralized, dispersed, high altitude, and long-distance transportation. The transportation process is not affected by natural conditions, ensuring that materials are not affected by moisture and are environmentally friendly and pollution-free. This equipment adopts a PLC control system, which can be automatically or manually controlled. After long-term practical operation, it has been proven that the equipment has stable performance, reliable quality, and no dust pollution during transportation. It is an ideal pneumatic conveying equipment.
PCD type positive pressure dense phase pneumatic conveying silo pump has seven advantages:
1. No pipe blockage
The pneumatic conveying bin pump can basically adapt to the pneumatic conveying of any powder material, and the system installed with the pneumatic conveying bin pump will not cause pipe blockage, with very high reliability. Even if you want to artificially block the pipes, it's a very difficult thing
2. Long distance pneumatic conveying
The warehouse pump can achieve ideal long-distance pneumatic conveying. Currently, in domestic cases, only the dense phase pneumatic conveying system operates stably with a conveying distance exceeding 2000 meters.
3. Low energy consumption
The conveying process of the warehouse pump only consists of three processes: feeding and pressurized conveying, omitting the step of pipeline blowing. The warehouse pump can achieve full pipe dense phase pneumatic conveying with low flow rate, and can stop conveying when there is no ash, which will not affect the next conveying process and will not block the pipeline
4. Low wear and tear
Because the flow rate of the warehouse pump is low, wear is actually proportional to the flow rate. The pneumatic conveying flow rate of the warehouse pump generally does not exceed 5m/s. Many customers who are not familiar with it generally have high conveying pressure, which increases wear. In fact, the pressure of pneumatic conveying is not related to wear. The higher the conveying speed of the material, the more severe the wear will be.
5. High efficiency
Environmental protection is also used for dilute phase pneumatic conveying, but we have to admit that for the same conveying project, the conveying capacity of the warehouse pump can be more than twice that of the dilute phase pneumatic conveying
6. Specific gravity
The concentrated phase pneumatic conveying of the combined pump has strong adaptability and can transport almost any powder.
7. Simple configuration
The configuration of the warehouse pump is very simple, and modular components can save a lot of costs.
Technical service
Engineering consulting
Based on our years of extensive engineering practical experience in different industries, we are able to provide clients with professional and multi-dimensional engineering consulting services related to grinding systems and pneumatic conveying systems. From the early stages of the project to the installation and debugging of the production line, until stable production and compliance, we can provide technical consulting services from multiple perspectives. As long as customers have needs, we will provide them with reasonable suggestions and superior solutions at a professional level to meet their expectations and meet their needs.
Engineering design
We have a professional technical team composed of high-quality talents such as experts, scholars, senior engineers, and master's students who have won the National Science and Technology Progress Award and participated in the formulation of relevant industry standards. The team members have over ten years of experience in large state-owned design institutes in the industry, and have rich engineering practical experience and theoretical foundation. We can provide professional and systematic engineering design services for customers in various industries related to grinding systems and pneumatic conveying systems, and provide a complete set of solutions in the field of powder engineering.
After-sale service
We have a long-term service team for the production line, with good technology and responsible after-sales service. All members have over 5 years of work experience and are able to provide timely, efficient, and comprehensive scientific after-sales service to customers. We can provide customers with after-sales service throughout the entire process of self engineering construction, production line equipment installation, production line debugging, until the production line meets the standards and reaches production capacity, solving various difficulties and miscellaneous problems encountered by customers, and providing thoughtful, meticulous, and comprehensive after-sales service.
Large Capacity Pneumatic Conveying Bin Pump Parameter Table
Conveying Material | Bulk Density (t/m3) | Model | PCD24/H | PCD26/H | PCD28/H | PCD30/H | Conveying Distance | |
Specification | 16~20m3 | 18~22m3 | 20~27m3 | 26~32m3 | Level (m) | Level (m) | ||
Pulverized Coal | 0.5 | Delivery Volume (t/h) | 50~80 | 60~90 | 65~110 | 80~130 | 200 | 20 |
Fly Ash | 0.75 | 75~125 | 85~130 | 95~160 | 125~190 | 200 | 20 | |
Limestone Powder/Mineral Powder | 0.8 | 80~130 | 90~140 | 100~170 | 130~200 | 200 | 20 | |
Cement/Raw Meal | 1 | 100~150 | 115~175 | 130~215 | 165~260 | 200 | 20 |
Long-distance Pneumatic Conveying Bin Pump Parameter Table
Conveying Material | Bulk Density (t/m3) | Model | PCD24/L | PCD26/L | PCD28/L | PCD30/L | Conveying Distance | |
Specification | 16~20m3 | 18~22m3 | 20~27m3 | 26~32m3 | Level (m) | Level (m) | ||
Pulverized Coal | 0.5 | Delivery Volume (t/h) | 20~40 | 25~45 | 30~55 | 45~65 | 1000 | 25 |
Fly Ash | 0.75 | 35~60 | 45~65 | 45~80 | 65~95 | 1000 | 25 | |
Limestone Powder/Mineral Powder | 0.8 | 40~65 | 45~70 | 50~85 | 70~100 | 1000 | 25 | |
Cement/Raw Meal | 1 | 50~80 | 55~90 | 65~110 | 90~120 | 1000 | 25 |
Conventional Grid Pneumatic Conveying Bin Pump Parameter Table
Conveying Material | Bulk Density(t/m3) | Model | PCD18/N | PCD20/N | PCD20/N | Reference Conveying Distance | |
Specification | 5.0~6.7m3 | 7.0~10.0m3 | 10.0~15.0m3 | Level (m) | Vertical (m) | ||
Pulverized Coal | 0.5 | Delivery Volume (t/h) | 12~20 | 16~32 | 25~50 | 500 | 30 |
Fly Ash | 0.75 | 18~32 | 25~48 | 35~70 | 50 | ||
Limestone Powder/Mineral Powder | 0.8 | 20~35 | 26~51 | 38~75 | 500 | 30 | |
Cement/Raw Meal | 1.0 | 24~42 | 32~65 | 48~95 | 500 | 30 | |
Silicon Powder | 1.2 | 28~50 | 40~75 | 55~115 | 500 | 30 |
Parameter Table Of Small Size Pneumatic Conveying Bunker Pump
Material | Bulk Density(t/m3) | Model | PCD08/M | PCD10/M | PCD12/M | PCD14/M | Reference Conveying Distance | |
Specification | 0.2~0.5m3 | 0.6~1.6m3 | 1.5~2.5m3 | 2.5~5.0m3 | Level (m) | Vertical (m) | ||
Pulverized Coal | 0.5 | Delivery Volume (t/h) | 0.5~1.8 | 1.5~5.5 | 5.0~9.0 | 8.0~18.0 | 100 | 20 |
Fly Ash | 0.75 | 0.9~2.8 | 2.5~8.5 | 7.0~14.0 | 12.0~27.0 | 100 | 20 | |
Limestone Powder/Mineral Powder | 0.8 | 1.0~3.0 | 3.0~9.0 | 8.0~15.0 | 12.0~28.0 | 100 | 20 | |
Cement/Raw Meal | 1.0 | 1.2~3.5 | 3.5~11.5 | 10.0~18.0 | 16.0~36.0 | 100 | 20 | |
Silicon Powder | 1.2 | 1.5~4.0 | 4.5~13.5 | 12.0~20.0 | 19.0~43.0 | 100 | 20 |