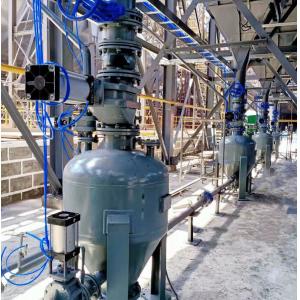
Add to Cart
New Type Over 300 t/h Conveying Capacity Pneumatic Conveyor Bin Pump For Fly Ash
Product Introduction:
The entire system of the positive pressure dense phase pneumatic conveying system consists of a Roots blower, manual plug valve, rotating feeding device, Venturi spraying device, conveying pipeline, pipeline diversion valve, as well as a storage bin, top dust removal device, electrical control system, and related auxiliary settings. The entire operating mode utilizes the positive pressure air flow generated by the Roots blower as the conveying power to transport the material continuously supplied by the rotary feeder from the lower hopper to the subsequent storage bin. The storage bin is equipped with a top dust removal device to separate the material and gas conveyed to the storage bin.
Advantages of PCD type positive pressure dense phase pneumatic conveying silo pump:
1. No pipe blockage
The pneumatic conveying bin pump can basically adapt to the pneumatic conveying of any powder material, and the system installed with the pneumatic conveying bin pump will not cause pipe blockage, with very high reliability. Even if you want to artificially block the pipes, it's a very difficult thing
2. Long distance pneumatic conveying
The warehouse pump can achieve ideal long-distance pneumatic conveying. Currently, in domestic cases, only the dense phase pneumatic conveying system operates stably with a conveying distance exceeding 2000 meters.
3. Low energy consumption
The conveying process of the warehouse pump only consists of three processes: feeding and pressurized conveying, omitting the step of pipeline blowing. The warehouse pump can achieve full pipe dense phase pneumatic conveying with low flow rate, and can stop conveying when there is no ash, which will not affect the next conveying process and will not block the pipeline
4. Low wear and tear
Because the flow rate of the warehouse pump is low, wear is actually proportional to the flow rate. The pneumatic conveying flow rate of the warehouse pump generally does not exceed 5m/s. Many customers who are not familiar with it generally have high conveying pressure, which increases wear. In fact, the pressure of pneumatic conveying is not related to wear. The higher the conveying speed of the material, the more severe the wear will be.
5. High efficiency
Environmental protection is also used for dilute phase pneumatic conveying, but we have to admit that for the same conveying project, the conveying capacity of the warehouse pump can be more than twice that of the dilute phase pneumatic conveying
6. Specific gravity
The concentrated phase pneumatic conveying of the combined pump has strong adaptability and can transport almost any powder.
7. Simple configuration
The configuration of the warehouse pump is very simple, and modular components can save a lot of costs.
Application Area
PCD pneumatic conveying equipment and systems have been widely used in industries such as building materials, chemicals, mining, power, and metallurgy. The conveying materials include cement, raw materials, fly ash, hydrated lime, dry discharged calcium carbide slag, slag powder, steel slag powder, coal powder, aluminum oxide powder, bauxite powder, phosphate powder, pyrophyllite powder, and organic silicon powder.
Large Capacity Pneumatic Conveying Bin Pump Parameter Table
Conveying Material | Bulk Density (t/m3) | Model | PCD24/H | PCD26/H | PCD28/H | PCD30/H | Conveying Distance | |
Specification | 16~20m3 | 18~22m3 | 20~27m3 | 26~32m3 | Level (m) | Level (m) | ||
Pulverized Coal | 0.5 | Delivery Volume (t/h) | 50~80 | 60~90 | 65~110 | 80~130 | 200 | 20 |
Fly Ash | 0.75 | 75~125 | 85~130 | 95~160 | 125~190 | 200 | 20 | |
Limestone Powder/Mineral Powder | 0.8 | 80~130 | 90~140 | 100~170 | 130~200 | 200 | 20 | |
Cement/Raw Meal | 1 | 100~150 | 115~175 | 130~215 | 165~260 | 200 | 20 |
Long-distance Pneumatic Conveying Bin Pump Parameter Table
Conveying Material | Bulk Density (t/m3) | Model | PCD24/L | PCD26/L | PCD28/L | PCD30/L | Conveying Distance | |
Specification | 16~20m3 | 18~22m3 | 20~27m3 | 26~32m3 | Level (m) | Level (m) | ||
Pulverized Coal | 0.5 | Delivery Volume (t/h) | 20~40 | 25~45 | 30~55 | 45~65 | 1000 | 25 |
Fly Ash | 0.75 | 35~60 | 45~65 | 45~80 | 65~95 | 1000 | 25 | |
Limestone Powder/Mineral Powder | 0.8 | 40~65 | 45~70 | 50~85 | 70~100 | 1000 | 25 | |
Cement/Raw Meal | 1 | 50~80 | 55~90 | 65~110 | 90~120 | 1000 | 25 |
Conventional Grid Pneumatic Conveying Bin Pump Parameter Table
Conveying Material | Bulk Density(t/m3) | Model | PCD18/N | PCD20/N | PCD20/N | Reference Conveying Distance | |
Specification | 5.0~6.7m3 | 7.0~10.0m3 | 10.0~15.0m3 | Level (m) | Vertical (m) | ||
Pulverized Coal | 0.5 | Delivery Volume (t/h) | 12~20 | 16~32 | 25~50 | 500 | 30 |
Fly Ash | 0.75 | 18~32 | 25~48 | 35~70 | 50 | ||
Limestone Powder/Mineral Powder | 0.8 | 20~35 | 26~51 | 38~75 | 500 | 30 | |
Cement/Raw Meal | 1.0 | 24~42 | 32~65 | 48~95 | 500 | 30 | |
Silicon Powder | 1.2 | 28~50 | 40~75 | 55~115 | 500 | 30 |
Parameter Table Of Small Size Pneumatic Conveying Bunker Pump
Material | Bulk Density(t/m3) | Model | PCD08/M | PCD10/M | PCD12/M | PCD14/M | Reference Conveying Distance | |
Specification | 0.2~0.5m3 | 0.6~1.6m3 | 1.5~2.5m3 | 2.5~5.0m3 | Level (m) | Vertical (m) | ||
Pulverized Coal | 0.5 | Delivery Volume (t/h) | 0.5~1.8 | 1.5~5.5 | 5.0~9.0 | 8.0~18.0 | 100 | 20 |
Fly Ash | 0.75 | 0.9~2.8 | 2.5~8.5 | 7.0~14.0 | 12.0~27.0 | 100 | 20 | |
Limestone Powder/Mineral Powder | 0.8 | 1.0~3.0 | 3.0~9.0 | 8.0~15.0 | 12.0~28.0 | 100 | 20 | |
Cement/Raw Meal | 1.0 | 1.2~3.5 | 3.5~11.5 | 10.0~18.0 | 16.0~36.0 | 100 | 20 | |
Silicon Powder | 1.2 | 1.5~4.0 | 4.5~13.5 | 12.0~20.0 | 19.0~43.0 | 100 | 20 |
In terms of positive pressure dense phase intermittent pneumatic conveying, the company has always been committed to theoretical research and engineering practice experience summary of pneumatic conveying systems, focusing on breaking through the key technologies of long-distance, high production, low energy consumption, and low wear in the pneumatic conveying process. The core product is the PCD type positive pressure dense phase pneumatic conveying silo pump, while providing systematic, standardized, and refined engineering design and technical services. To meet the needs of different customers, we create the best design plan based on parameters such as material properties, conveying distance, conveying capacity, receiving warehouse capacity, dust removal capacity, and geographical conditions. Each equipment is manufactured through qualified inspection, and each pneumatic conveying system has its own design features, allowing customers to truly experience the intelligent management and economic benefits brought by advanced technology products.
At present, our longest conveying horizontal distance is 2200m and the height is 30m; The maximum conveying capacity of a single unit is 300 t/h; The transportation energy consumption is less than 3.8kWh/t · km, the service life of the straight pipeline is more than 10 years, and the service life of the elbow is more than 3 years. We develop the best engineering design and equipment selection plan based on customer requirements and parameters such as powder material specifications, performance, transportation distance, transportation volume, and geographical conditions provided by the customer, such as air volume calculation, pipeline ratio, dust collection treatment in the receiving warehouse, and after-sales plan. Based on extensive engineering practice experience, most of the positive pressure dense phase intermittent pneumatic conveying processes are mainly divided into the following three processes:
Main features of the product
① Large conveying capacity: > 300t/h;
② Long distance: > 2000m;
③ Low power consumption: < 3.8kWh/t · km;
④ Low wear and tear: pipeline life>10 years;
⑤ Low speed: initial speed 6-10m/s;
⑥ High mixing ratio: > 30kg/kg;
⑦ Flexible process layout, dust-free, high operation rate, lower investment compared to mechanical conveying, and lower maintenance costs