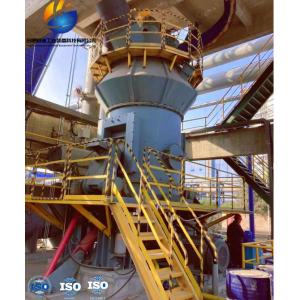
Add to Cart
Gypsum Grinding Mill Dedicated to Desulfurization Gypsum Powder Production Line Equipment
Gypsum powder is a non-metallic mineral with high market value, widely used in various fields such as construction, building materials, power plants, papermaking, paint, food, medicine, etc. Unlike natural gypsum, desulfurization gypsum powder, as an industrial solid waste, also has recycling value. By using desulfurization gypsum powder production line equipment, waste can be turned into treasure and value can be created. Vertical grinding machine is a specialized mill that helps bring greater value to the field of desulfurization gypsum.
Specifications And Technical Parameters Of HVM Gypsum Vertical Mill
Model | HVM2500 | HVM2800 | HVM3400 | HVM3700 | HVM4200 | HVM4500 | HVM4800 | HVM5100 | HVM5600 |
Grinding Table Median Diameter(mm) | 2500 | 2800 | 3400 | 3700 | 4200 | 4500 | 4800 | 5100 | 5600 |
Capacity(t/h) | 85-100 | 130-160 | 190-240 | 240-300 | 320-400 | 400-500 | 440-550 | 550-670 | 600-730 |
Raw Material Moisture | <10% | ||||||||
Raw Meal Fineness | R0.08<12% | R0.08<14% | |||||||
Raw Meal Moistrue | ≤1% | ||||||||
Main Motor Power(kW) | 800/900 | 1120/1250 | 1800/2000 | 2500/2800 | 3150/3350 | 3800/4200 | 4200/4500 | 5000/5400 | 5600/6000 |
Illustrate | Re:Raw materials bond index≤13kWh/t |
1. Understand desulfurization gypsum and equipment together
At present, the most mature desulfurization method for thermal power plants is the limestone gypsum method. In order to improve the efficiency of flue gas desulfurization, high requirements are placed on the calcium oxide content and fineness of limestone powder used for desulfurization in the desulfurization process technology. With the expansion of the gypsum market, the price of gypsum powder is also constantly increasing, and the number of projects for grinding gypsum powder is not constantly increasing.
Working principle: The electric motor drives the grinding disc to rotate through a reducer, and the material falls into the center of the grinding disc from the feeding port. At the same time, hot air enters the grinding chamber from the air inlet. Under the action of centrifugal force, the material moves towards the edge of the grinding disc and is crushed by the grinding roller when passing through the circular groove on the grinding disc. The crushed material is carried up by the high-speed airflow at the edge of the grinding disc, and large particles directly fall onto the grinding disc for re grinding. When the material in the airflow passes through the dynamic and static separator, under the action of the rotating rotor, the coarse powder falls onto the grinding disc for re grinding, and qualified fine powder is discharged with the airflow, Collect in the powder collection device, which is the product. Materials containing moisture are dried during contact with hot gases to achieve the required product moisture.
2. Vertical mill and its advantages for desulfurization market
Vertical grinding equipment is one of the ideal grinding and processing equipment. Hefei Hengcheng responds to the call for energy conservation and emission reduction, assisting in the efficient grinding and processing of solid waste such as limestone desulfurization and desulfurization gypsum in coal mines, thermal power plants, metallurgy, building materials, and many other markets.
The vertical mill integrates crushing, grinding, grading, drying, conveying, and powder collection, with high grinding efficiency, high production rate, low energy consumption, larger feed particle size, energy conservation, and emission reduction. It is currently a specialized grinding equipment in the field of dry powder production. Its advantages and characteristics can be summarized as follows:
(1) Environmental noise reduction
Vertical grinding equipment has low vibration, low noise, full negative pressure operation, and no dust leakage, making it a specialized equipment that is conducive to enhancing market competitiveness.
(2) Reliable performance
The grinding roller limit device can avoid vibration caused by material breakage. New grinding roller sealing device, with better sealing performance.
(3) High powder yield
High grinding efficiency and high single machine productivity.
(4) Energy saving
Low energy consumption, compared to ball mills, it is 40-50% lower in energy consumption.
(5) Strong drying power
It can directly blow hot air and has strong drying ability, without the need to purchase an additional dryer. The feed moisture can reach up to 15%.
(6) Low investment
The process flow is simple, the system equipment is few, the layout is compact, the floor area is small, and it can be arranged outdoors to reduce comprehensive costs.
(7) Automated operations
Adopting a PLC fully automatic control system for remote control and easier operation.