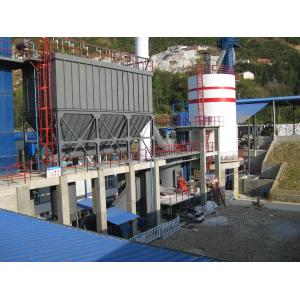
Add to Cart
Bentonite Grinding Moisture ≤1% Bentonite Grinding Mill For Bentonite Output Plant
Description
Bentonite is a mineral with very high application value. It is widely used in building materials because of its good expansion, water absorption, adhesion and pulping properties, which greatly enhances the performance of building materials.
In order to maximize the use of bentonite, we need to use a pulverizer to grind the bentonite into powder. The motor of the bentonite vertical mill drives the grinding disc to rotate through the reducer. . Under the action of centrifugal force, the material moves to the edge of the grinding disc, and is crushed by the grinding roller when it passes through the annular groove on the grinding disc. Re-grinding, when the material in the airflow passes through the dynamic and static separator, under the action of the rotating rotor, the coarse powder falls on the grinding disc for re-grinding, and the qualified fine powder is milled together with the airflow and collected in the powder collecting device, which is product. Moisture-containing materials are dried during contact with hot gas to achieve the required product moisture.
As a well-known manufacturer of non-metallic mineral grinding equipment industry, the bentonite vertical mill produced by Hefei Hengcheng Industrial Equipment Technology Co., Ltd. is deeply loved by major powder manufacturers. It has the advantages of energy saving; environmental protection; high efficiency; high operation rate (99% guarantee rate); high output and low consumption, strong adaptability, wide application range; more than 15 years of continuous research and development and innovation, to provide owners with comprehensive and practical solutions, etc. It is the preferred equipment for grinding bentonite.
Solution
(1) Material moisture
Existing problems: cakes are easily generated on the grinding disc due to the high pressure of the grinding rollers.
Solution: Introduce hot air during the grinding process; install a special grinding disc scraping device at the front end of the material entering the rolling area of the grinding roller. -2.5cm.
(2) The grinding temperature of the mill
Existing problems: the air temperature entering the mill is too low, the drying capacity of the mill is insufficient, resulting in low grinding efficiency, and the material layer of the grinding disc becomes thicker, resulting in a large current of the mill; the air temperature is too high, resulting in low water output from the mill, which seriously reduces the performance of the product. If the temperature of the air entering the mill exceeds 300 °C, the bentonite will begin to lose crystal water, and the microstructure will change, affecting the activity or even deactivation.
Solution: The temperature of the air entering the mill is controlled at 140-160℃, and the temperature of the air exiting the mill can be controlled at 50-60℃. The moisture content of the product is basically 8%-12%, which will not affect the intrinsic activity of the powder.
(3) The height of the disc stopper ring
Existing problems: the height of the stopper ring is too high, resulting in excessive grinding and increased energy consumption; the height of the stopper ring is too low, which will increase the slag discharge of the mill, which may cause the circulation elevator to block;
Solution: Reduce the height of the stopper to 2cm, which is conducive to the rapid overflow of the surface powder from the grinding disc and is carried away by the wind, reducing the thickness of the material layer, the current of the mill is reduced and stabilized, the output of the mill is significantly improved, and the vibration is also very slight.
(4) Wind speed of grinding disc wind ring
Existing problems: too small wind speed and insufficient material carrying capacity will lead to large slag discharge and low output of the mill; too high wind speed will result in less slag discharge and increased circulation in the mill, which is not conducive to the fine sorting of finished products.
Solution: In production, it can be inferred whether the wind speed of the air ring is reasonable according to the amount of material returned by the mill. If the amount of slag returned is large, the air ring gap can be appropriately reduced, the wind speed at the air ring can be increased, and the material carrying capacity can be increased, so as to achieve the effect of increasing production and reducing emissions; As long as the current of the mill allows, increasing the pressure of the grinding roller can continue to increase the production.
Technical Data
Specifications | HVM800 | HVM1250 | HVM1300 | HVM1500 | HVM1700 | HVM1750 | HVM1900 | HVM2400 | HVM2400 | HVM2500 |
Grinding table median diameter | 800 | 1250 | 1300 | 1500 | 1700 | 1750 | 1900 | 2400 | 2400 | 2500 |
Capacity(t/h) | 1-3 | 2-7 | 3-12 | 4-16 | 6-24 | 7-27 | 7-28 | 9-35 | 10-39 | 11-45 |
Materials Grain Size(mm) | 0-15 | 0-20 | 0-25 | 0-35 | 0-35 | 0-35 | 0-40 | 0-40 | 0-40 | 0-50 |
Materials Moisture(%) | <5 | |||||||||
Product Fineness(10-40um) | 97% | |||||||||
Product Moisture(%) | ≤1 | |||||||||
Main Motor Power(kw) | 55 | 132 | 180 | 250 | 355 | 400 | 450 | 560 | 630 | 710 |
Re:The data based on Mohs'hardness 3-4 material
The product fineness can reach 10 um(1250 meshes)
Product advantages:
1. The superfine vertical mill adopts the principle of high-efficiency and energy-saving material layer grinding, with high grinding efficiency and low energy consumption; the single machine has a large production capacity and can utilize low-valley electricity; the vertical grinding technology and equipment are new energy-saving and consumption-reducing technologies vigorously advocated by the state. , which is conducive to enhancing the competitiveness of enterprises in the powder industry in this region and even the whole country;
2. Strong applicability and low investment Adopt secondary classification to realize multi-purpose of one machine, strong practicability of equipment, and save investment cost.
3. The product quality of calcite ultrafine vertical mill is stable
(1) The material stays in the pulverizer for a short time, and it is easy to detect the particle size distribution and composition of the product, and the product quality is stable;
(2) The product has uniform particle shape, narrow particle size distribution, good fluidity and strong product adaptability;
4. Easy maintenance and low operating cost
(1) The grinding roller can be turned out of the machine by hydraulic device, the replacement of the roller sleeve lining plate and the maintenance space of the grinding machine are large, and the maintenance operation is very convenient;
(2) The roller sleeve can be turned over for use, which prolongs the service life of the wear-resistant material;
5. Environmental protection
(1) The whole system of HLM vertical mill has small vibration and low noise;
(2) The system is sealed as a whole, operates under full negative pressure, and has no dust spillage, which can basically realize a dust-free workshop;
6. Low wear, grinding rollers and disc linings are made of special materials and have a long service life;
7. The calcite ultrafine vertical mill has a high degree of automation: the automatic control technology adopts the German Siemens series PLC, equipped with an automatic control system, which can realize remote control and easy operation. The workshop can basically realize unmanned operation and save operating costs.
8. There is no need to put cloth on the grinding disc before starting the calcite ultra-fine vertical mill, and the mill can be started with no load, eliminating the trouble of difficult starting;