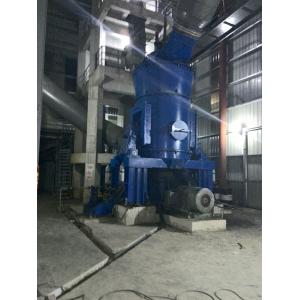
Add to Cart
3 Roller Ultrafine Gypsum Limestone Stone Powder Vertical Grinding Mill Machine
Description:
With the rapid development of society and economy, in the field of ultra-fine powder processing, in the face of more and more application requirements for ultra-fine powder, traditional ultra-fine powder processing equipment has been difficult to meet market demand due to its generally low production capacity.
After painstaking research, we designed and developed an advanced grinding equipment that is safe, environmentally friendly, energy-saving and efficient, and integrates drying, grinding, powder selection and conveying functions. The main performance and economic and technical indicators of the equipment have reached the international advanced level.
HVM vertical mill can be widely used in chemical, metallurgical, non-metallic ores and other industries, especially in the field of ultra-fine grinding of white non-metallic ores. The industry provides high quality fillers and additives. It can be widely used in large-scale ultra-fine dry powder processing of non-metallic minerals such as calcite, marble, limestone, dolomite, barite, talc, kaolin, dolomite, wollastonite, gypsum, feldspar, and pyrophyllite.
Specifications And Technical Parameters Of HVM Gypsum Vertical Mill
Model | HVM2500 | HVM2800 | HVM3400 | HVM3700 | HVM4200 | HVM4500 | HVM4800 | HVM5100 | HVM5600 |
Grinding Table Median Diameter(mm) | 2500 | 2800 | 3400 | 3700 | 4200 | 4500 | 4800 | 5100 | 5600 |
Capacity(t/h) | 85-100 | 130-160 | 190-240 | 240-300 | 320-400 | 400-500 | 440-550 | 550-670 | 600-730 |
Raw Material Moisture | <10% | ||||||||
Raw Meal Fineness | R0.08<12% | R0.08<14% | |||||||
Raw Meal Moistrue | ≤1% | ||||||||
Main Motor Power(kW) | 800/900 | 1120/1250 | 1800/2000 | 2500/2800 | 3150/3350 | 3800/4200 | 4200/4500 | 5000/5400 | 5600/6000 |
Illustrate | Re:Raw materials bond index≤13kWh/t |
【Advantage】
Energy Efficient
Under the condition of the same finished product fineness and motor power, the output is more than double that of jet mill, stirring mill and ball mill.
Long Service Life Of Wearing Parts
Grinding rollers and grinding rings are forged with special materials, which greatly improves the utilization.
High Safety And Reliability
Because there is no rolling bearing and no screw in the grinding chamber, there is no problem that the bearing and its seals are easily damaged, and there is no problem that the screw is easy to loosen and damage the machine.
Environmentally Friendly And Clean
The pulse dust collector is used to capture dust, and the muffler is used to reduce noise, which is environmentally friendly and clean.
【Working Principle】
The motor drives the grinding disc to rotate through the reducer, the material falls into the center of the grinding disc from the feed inlet, and the hot air enters the mill from the air inlet. Under the action of centrifugal force, the material moves to the edge of the grinding disc, and is crushed by the grinding roller when passing through the annular groove on the grinding disc. The crushed material is carried by the high-speed airflow at the air ring at the edge of the grinding disc, and the large particles fall directly on the grinding disc. Re-grinding, when the material in the airflow passes through the dynamic and static separator, under the action of the rotating rotor, the coarse powder falls on the grinding disc for re-grinding, and the qualified fine powder is ground together with the airflow and collected in the powder collecting device, which is product. Moisture-containing materials are dried during contact with hot gas to achieve the required product moisture.